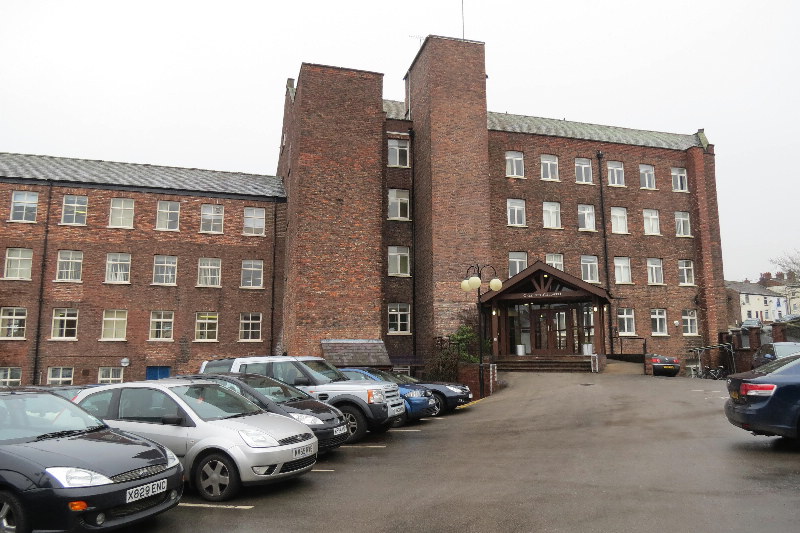
Before our visit to Paradise Mill and the Silk Museum, Elizabeth gave me a quick tour of Victoria Mill, the office building where she works.
|
We bought tickets at the Silk Museum (at left). Then our guide led us to Paradise Mill...
|
...and up the stairs to where the looms are set up.
|
After some introductory remarks about silk moths and the history of silk weaving, the first machine we saw was designed to transfer the warp threads to a giant reel. Note all the blue spools of silk thread in the background. Note too how narrow the section is as it reaches the reel. Silk thread is very fine!
|
Here's a better view of all the spools. The white cloth is there so the operators can see when a thread breaks and quickly repair it before it affects the warp.
|
Because the thread is so fine, special tools are needed to feed it through narrow channels before it reaches the reel.
|
This machine was used to transfer thread from skeins to spools.
|
Here are several of the mill's Jacquard Looms.
|
A closer view of a loom. Shuttle at the left. You can just see a part of the foot treadle below. Everything was human powered. An operator could weave roughly forty threads per minute and keep up the pace for hours.
|
Atop the loom is the Jacquard device, essentially a computer reading punched cards that determined which warp threads would be up and which down when the shuttle was passed through. You can see the cards to the left and below the device. Hundreds of cards were used for a pattern, attached by cord to each other in an endless loop.
|
This machine was set up with just four cards to show how it worked.
|
Back to the loom, finished cloth is at the left; the warp behind and to the right.
|
Several possibilities come to mind as explanations for the shape and hole in the operator's bench. No, it wasn't because they weren't allowed bathroom breaks. Leather straps over the depression would have been present to offer a bit of cushioning and the hole was used to hold the board while the operator slid into position.
|
Some broader views of the workspace.
|
In operation, it would be much more crowded.
|
A stack of punch card programs for various patterns.
|
In the office, we saw original drawings that were the basis for patterns.
|
Patterns were then painted, square by square, onto a sort of graph paper. These patterns then went to an operator trained to transfer this information to the punch cards. Each card was numbered and they were all sewn together. When complete, the programs were run through the loom once to check for errors. If an error was found, a new card had to be made and inserted in place of the incorrect one. It was also possible to fill or punch holes right on the machine if the error was a small one or the card became damaged.
|
Even the office was kept as it was when the mill closed.
|
After leaving the mill, we toured the Silk Museum. Macclesfield silk mills switched from decorative materials to parachute silk in WWII.
|
Several special purpose power looms were on display...
|
...including this ribbon loom.
|
Multiple looms in miniature wove complex patterns into the ribbons.
|
There were two large picture looms on display.
|
Picture Looms wove patterns like this. (This is the artist's pattern for one; the finished picture would be much smaller.)
|
|